
- #Resistance to temperature conversion table software#
- #Resistance to temperature conversion table mac#
Perfect Partner for Development of Encoder controlled Stepper Motor Actuators. If I could give 6 stars for customer service - I would do so. Customer service gave me first class service. I had a weird problem - it did not work on one of my PC’s. PicoLog TC-08: This is a very nice unit that works consistently and reliably. We have been using Picoscope 6404D for quite some time, and are amazed by its accuracy and powerful emulations while working with numerous signal evaluations. This made my decision much easier when I was looking to buy an USB scope.
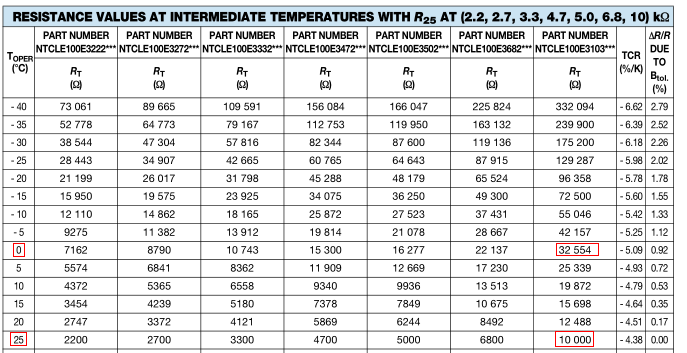
#Resistance to temperature conversion table mac#
Not many USB scopes works on Win & Mac & Linux too, so that proves me that guys from Pico really cares about us, customers. Storage of waveforms on my Laptop is very easy allowing me to quickly email waveforms to my Colleagues. I travel abroad so this has been ideal due to its physical size. I have been using my 4224 PicoScope for years. Superb kit, superb support, what more can I say.
#Resistance to temperature conversion table software#
The kit (2408B) is of obvious quality, easy to setup and calibrate and the free to download software has a reasonable learning curve. Most equipment can cope with up to 100 ohms per core. When using long cables, it is necessary to check that the measuring equipment is capable of handling the resistance of the cables. Using screened cable, with the screen grounded at one end, may help to reduce interference. Similarly, a 1 ♚ error in the sense current will give 0.4 ☌ temperature error.īecause of the low signal levels, it is important to keep any cables away from electric cables, motors, switchgear and other devices that may emit electrical noise. For example, a 100 µV voltage measurement error will give a 0.4 ☌ error in the temperature reading. Because the change in resistance for a degree celsius is very small, even a small error in the measurement of the voltage across the sensor will produce a large error in the temperature measurement. Using a 1 mA sense current will give a signal of only 100 mV. This effect can be reduced by either using a large sensor element, or by making sure that it is in good thermal contact with its environment. If the sensor element is unable to dissipate this heat, it will report an artificially high temperature. The current through the sensor will cause some heating: for example, a sense current of 1 mA through a 100 ohm resistor will generate 100 µW of heat. It is also possible to obtain three-wire sensors, although these operate on the (not necessarily valid) assumption that the resistance of each of the three wires is the same. For precision work, sensors have four wires- two to carry the sense current, and two to measure the voltage across the sensor element. Rt is the resistance at temperature t, R0 is the resistance at 0 ☌, andįor a PT100 sensor, a 1 ☌ temperature change will cause a 0.384 ohm change in resistance, so even a small error in measurement of the resistance (for example, the resistance of the wires leading to the sensor) can cause a large error in the measurement of the temperature. The most recent definition of the relationship between resistance and temperature is International Temperature Standard 90 (ITS-90). For precision measurement, it is necessary to linearise the resistance to give an accurate temperature. The relationship between temperature and resistance is approximately linear over a small temperature range: for example, if you assume that it is linear over the 0 to 100 ☌ range, the error at 50 ☌ is 0.4 ☌.
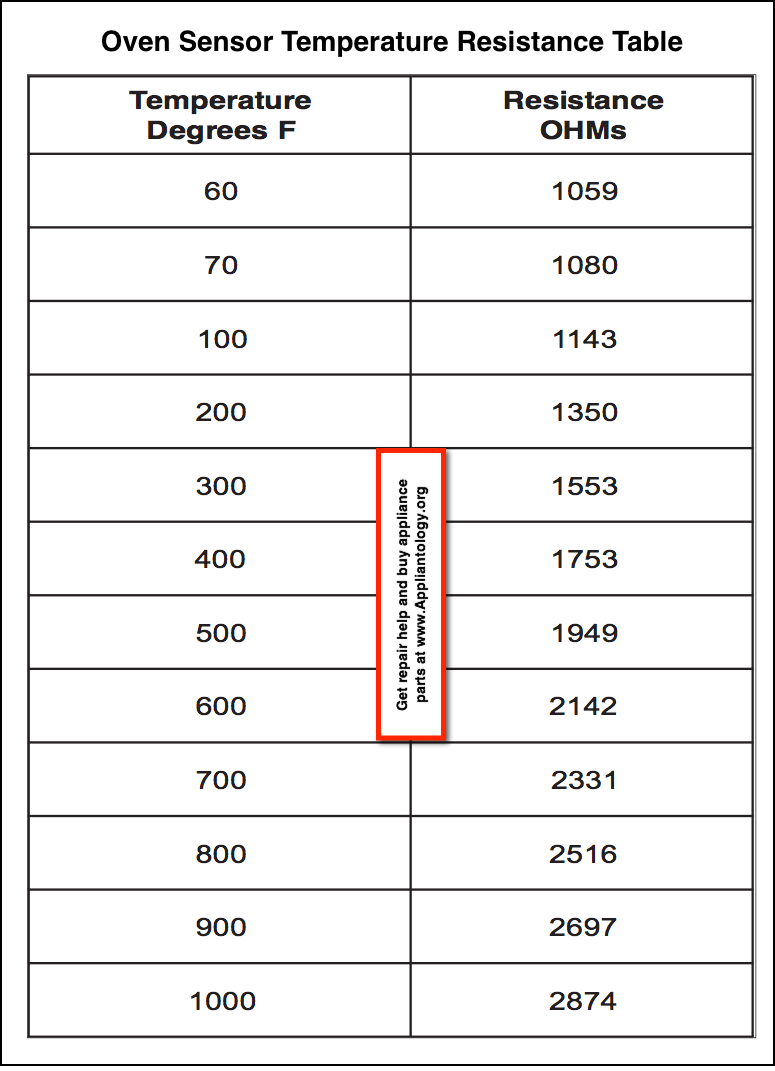


There are also PT1000 sensors that have a resistance of 1000 ohms at 0 ☌. The most common type (PT100) has a resistance of 100 ohms at 0 ☌ and 138.4 ohms at 100 ☌. The principle of operation is to measure the resistance of a platinum element. Unlike thermocouples, it is not necessary to use special cables to connect to the sensor. Standard sensors are are available from many manufacturers with various accuracy specifications and numerous packaging options to suit most applications. Platinum resistance thermometers (PRTs) offer excellent accuracy over a wide temperature range (from –200 to +850 ☌).
